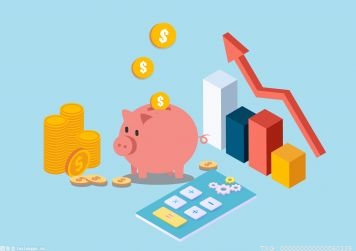
深化成本工程实施,推进提质增效发展。集团多次强调,要以正向研发为依托实施正向成本管理,从产品研制的全流程出发,在推动成本工程向业务深层次、细末节方面再发力。
(相关资料图)
2022年收官在即,中国航发南方和中国航发黎明围绕生产全过程和修理全流程持续优化方案,聚焦技术攻关升级,积极开展成本工程,降本增效成效明显。
中国航发南方
以技术升级推动生产降本
2022年,中国航发南方强管理、稳生产,深入推进实施成本工程,聚焦产品研制全流程,从设计制造协同、生产过程控制、工艺技术提升等维度一体推进成本管理,降本增效推动高质量发展。
源头协作降成本
公司以型号成本为出发点,确定年度成本压降目标,建立设计制造协同降本地图,从设计源头开展型号全价值链专项降本。结合工业化鉴定(DVI)工作开展成本控制,将降本工作理念细化至每道加工工序。在前期研讨分析阶段,制定铸件成型及加工合格率提升等专项计划,针对性开展制造成本控制探索。在型号状态鉴定阶段,开展工艺技术攻关,减少状态变更节约成本。围绕型号修理环节,持续开展发动机零部件修理降本方案研究,降低零件报废数量,进一步压降成本。
周期压减显成效
先进合理的生产期量标准能准确确定产品投入产出时间,加强生产过程管理。2022年,南方成立生产周期管控专项团队,以关键型号为试点,对周期管控现状及堵点进行分析研判。同时制定专项管控方案和改进措施,动态调整期量标准。针对长周期零组件设置关键工序控制点,聚焦全流程监控,一体把控生产订单从投入到产出的全生命周期。针对修理机,公司则将各环节划分为准备作业、修理作业、出厂作业三大模块,拉通MES、物流、试车三大系统,在完成数据集成的同时实现唯一数据源,让修理全过程显性化,该型号修理周期进一步缩短,修理成本有效下降。
工艺改进提质效
以工艺技术升级推动生产降本是持续提升创效能力的有力举措。南方聚焦技术提效,深入推进车铣、铣车等复合加工工艺研究,组织对铝镁机匣家族、动力涡轮盘家族、输出轴家族等17个零件家族、数十个图号零件开展改进,通过优化加工路线、加工方式、数控程序,实现部分手动操作及特种工艺替代,主轴转速与进给速率进一步提升,在线测量复合工序进一步集成,加工效率提升20%以上。
中国航发黎明
技术升级再造维修新体系
航空发动机修理过去往往存在换件成本高、采购备件难、修理深度不足等问题,修理成本高、交付进度慢。
为解决这一突出问题,中国航发黎明大修厂与中国航发动力(600893)所组建专项团队,以提高产品修理质量和效率,缩短交付周期为目标,围绕修理全流程,系统梳理修理关键点,对零部件的修理标准、修理周期、更换件比例、深度修理等方面开展全方位调研,优化修订修理标准,全面梳理产品在故检、修理、装配环节的成本构成,集中整合技术和制造能力,制定优化措施和修理攻关项目,进一步降低整机修理成本。
优化修理技术标准
专项团队对产品修理中的换件率、修理周期、深度修理等内容进行梳理,对标低成本项目,分析差异情况,提出修改完善需求,形成标准优化需求清单。
组织修理技术攻关
专项团队基于产品故检修理过程中的零件换件率情况,开展头脑风暴、集智攻关,梳理全流水件号,以公司级攻关、厂级攻关、修理工艺改进项等方式优化修理项目,将攻关成果纳入流程文件固化。
完善修理制度流程
专项团队不断完善管理制度,建立科研攻关成果工程化应用的保障、监督管理和奖励机制,对成果应用情况持续跟踪,最终形成一套成本清晰可控的体系流程,便于长效化开展成本压降工作。
段 蓉
曹立斌
牟鹏宇
核稿:焦静波
标签: